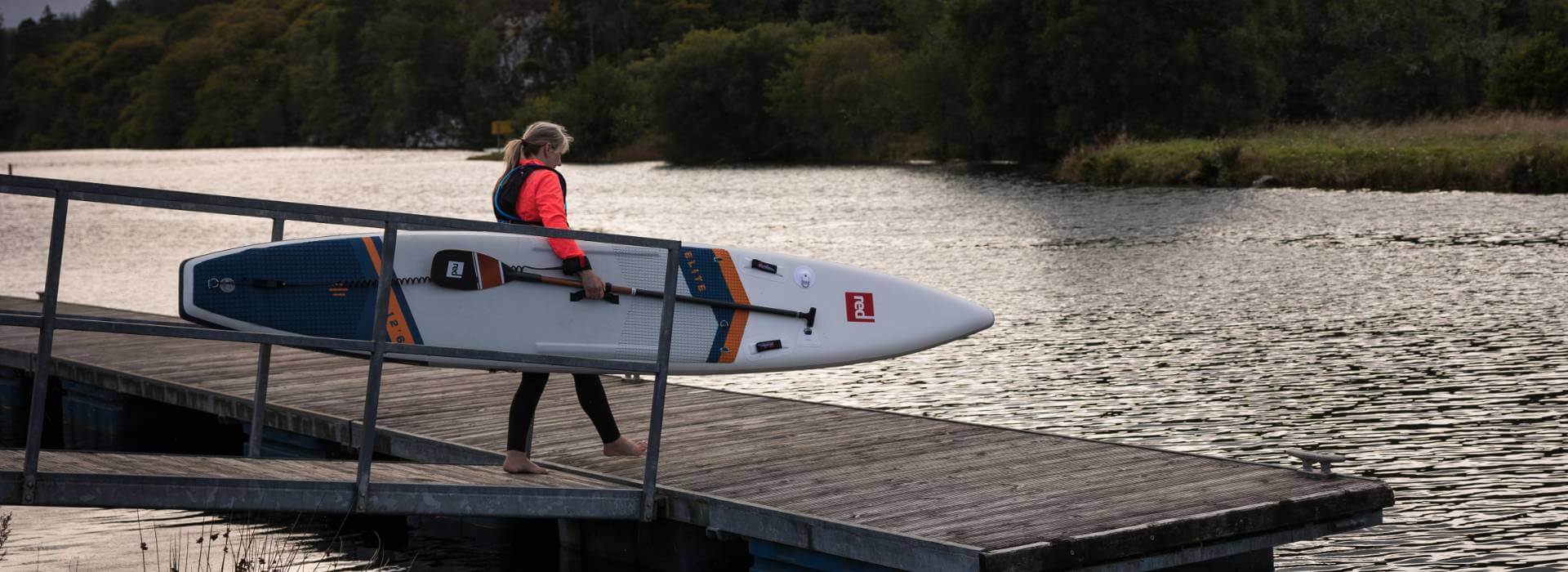
10 Ways To Improve Your SUP Racing Technique
Whether you’re just starting out in the SUP racing scene or have years of experience, this guide will help you improve your SUP racing technique.
Written by Maxine Smiles -Cooke /
Your bag is currently empty.
Creating an account has many benefits: